As published in Manufacturing Engineering
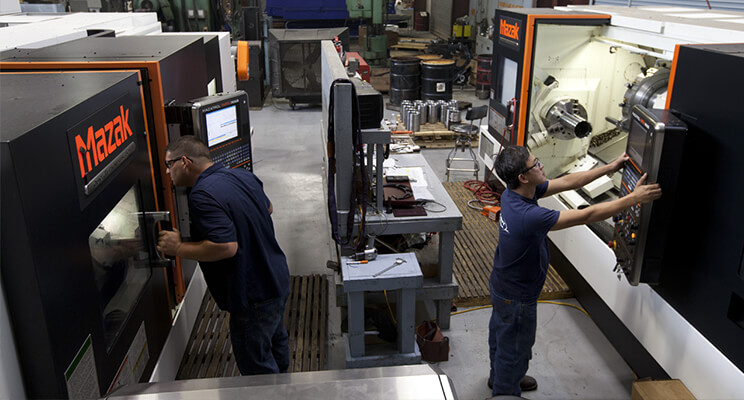
When Claude Barber, founder of Plant Machine Works Inc. in Baton Rouge, LA, passed away in 2006, his son Tom (Tommy) Barber officially took ownership of the shop that, at the time, specialized in repair work for the petrochemical and paper mill industries. While Tommy had basically zero experience in the day-to-day operations of the shop—having instead pursued a career in teaching and coaching sports—he successfully continued and expanded upon his father’s legacy to build Plant Machine Works into a shop that stands out from the competition by way of its large-part machining capabilities.
Tommy Barber, now owner and president, desperately wanted to differentiate the shop when he transitioned it into one that provided machining services as well as the established repair work. While doing so, he believed that the key to success would be to offer a niche machining service. In determining what that should be, he looked closely at all the other general machine shops in the immediate area. What he found was that all of them had small and medium-size machines, so, he decided the shop’s niche would be to go big, literally, and he acquired one of the largest CNC horizontal boring mills with a 78″ (1981-mm) table and 55,000-lb (24,948-kg) workpiece capacity. At the time, it was the biggest machine of its kind in the state.
Barber’s initial plan with the machine was to pursue lineboring work in the large-gearbox market—gearboxes as big as a 15 × 15′ (4.5 × 4.5-m) room. However, six months prior to actual installation and as the shop prepared for the huge new machine, the word got out, and Barber’s phone began to ring non-stop with incoming work requests.
“The machines have not only significantly improved part accuracy, they’ve allowed us to continuously reduce our turnaround times.”
“Every major oil company imaginable called,” said Barber. “Before our boring mill was even on the ship making its way to the United States, we had purchase orders to machine large parts, none of which had anything to do with gearboxes. And ironically, that particular machine, to this day, has never actually line bored a gearbox, nor have the other two huge boring mills we’ve since purchased.”
As the shop’s large-part machining business—mostly milling work—continued to surge, Plant Machine Works grew to its current 73 employees and 55,000 ft2 (5110-m2) facility with an increasing number of these existing customers requesting that the shop also do large-part turning work for them as well.
So in keeping with its newly established large-parts-making niche, Plant Machine Works invested in a turning machine with more advanced capabilities than an old legacy lathe it had in the repair side of the business. Unfortunately, this big newer CNC two-axis lathe with 160″ (4-m) long bed fell short when it came to rigidity and durability. Thus, part accuracy suffered.
This is when Barber acquired the shop’s first Mazak machine, a Slant Turn Nexus (STN) 500 turning center from Mazak distributor Dixie Mill in New Orleans. Then shortly afterwards, he added a Quick Turn Nexus QTN 350 and a QTN 450, both CNC turning centers also from Mazak. The machines provide Plant Machine Works with unmatched productivity and reduced cycle times across its wide range of shorter and longer, large-diameter shaft-type part applications.
The STN 500 started the ball rolling. Plant Machine Works quickly made the AVLs (approved vendor lists) of practically all of its major local customers for large part turning. These same customers would then have the shop also handle the turning work for all their other divisions located nationwide. Requests for quotes came in not only for big turning work but also for slightly smaller parts, those with 16–23″ (406–584mm) ODs and measuring 16–120″ (406–3048-mm) long, as opposed to the shop’s usual parts that ran much bigger. The QTN 350 and QTN 450 machines were acquired to machine these smaller part size jobs.
The STN 500 gives the shop a bed length of 120″ and allows it to machine part diameters up to 35.8″ (909 mm), as well as quickly create machining programs to run first article parts. The machine’s Nexus CNC control not only allows for fast and easy conversational or EIA/ISO programming formats, but also provides 3D machining simulation to verify part programs and check for possible interference with the machine’s turret and tailstock.
“Once we had the first Mazak up and running, we knew that any future turning machines we purchased were going to be Mazaks, which is why we got the two QTN machines,” said Barber. “The machines have not only significantly improved part accuracy, they’ve allowed us to continuously reduce our turnaround times. With their strength and power, we can take faster, more aggressive cuts to reduce cycle times, get parts off machines faster and open up additional machining capacity to take on even more work. And thanks to the Mazaks, we are able to manufacture and thread rotary shoulder connections, tubing, casings and drill stem elements to stringent customer supplied specifications.”
Many parts are oilfield components, and some are for coal burning plants. Cycle times can range from four minutes to those that will require a week’s worth of machining. Most of these big parts involve machining away huge amounts of material and holding tolerances between 0.0005 to 0.001″ (0.013–0.03 mm).
Practically all the shop’s energy industry customers provide their own raw material because of industry quality specifications and traceability requirements. A lot of these materials are modified carbon steels, some of which are quite challenging to machine. One is a 4340 +V. This newer oilfield material incorporates vanadium, making it extremely abrasive on cutting tools. To machine the material, Plant Machine Works employs special tooling that the shop has discovered performs better when run at more aggressive feed rates and taking heavier depths of cut that only the Mazaks can handle.
“Most machine tools lack the speed, power and rigidity to withstand the punishing parameters for long periods of time,” said Barber. “For instance, our QTN 450 easily handles machining a large long shaft part made from 4340 +V. This particular part involves a lot of material removal from its 14″ [355-mm] OD and along its entire 118″ [3-m] length. The challenge is the part’s length, and the machine’s heavy-duty rigid headstock and steadyrest play critical roles in preventing cutter chatter to ensure size and surface finishes are maintained.”
On the STN 500, the shop handles another challenging part for the oil and gas industry. The part starts as a solid large-diameter bar of tough 4140 with a trepanned ID hole through its length when loaded into the STN 500. The machine cuts 5″ (127-mm) worth of material from the part’s ID to generate two different diameters and an internal cone-shaped taper. Then it machines about 0.500″ from the part’s OD, drills some holes and does a threading operation. Total machining time for the part is 24 hours, which is a significantly faster processing time than if the part was done using the shop’s other equipment.
Barber refers to the Mazaks as “difference makers” in that they help the shop differentiate itself from the competition in terms of capabilities, particularly when it comes to machining speed. He said that, simply put, the Mazaks cut parts faster, and as an example, he cited a spacer part for which the QTN 350 drastically reduced processing time. With its older existing equipment, the shop completed the spacer part in 11 hours. The QTN 350 now finishes the part in just four minutes, and the machine’s processing speed and efficiency have opened up more opportunities in a slightly smaller part size range for the shop within other sectors of the energy industries it serves.
The capabilities of the QTN 350 also help reduce cycle times for another recently acquired energy industry job. The part is a mechanical inner sleeve. The QTN 350 machines the OD and ID on one half of the part, which is then flipped around for the other half to be machined. It also gets some grooves and threads cut in it then moves to another machine in the shop for some holes and slots. Previously, the turning and threading operations took 1.5 hours. Now, the QTN 350 does them in only 40 minutes.
Plant Machine Works is API licensed to cut and monogram threads under Specs. 5CT and 7-1, registered API Spec. Q1 and has ISO 9001:2008 and ISO/TS 29001 certifications. The shop has a fully calibrated quality control department that ensures all part requirements are fulfilled, and its welding shop is qualified in over 50 welding procedures for a variety of material types from carbon to stainless steel to titanium.
Plant Machine Works currently ships, on average, 200 completed jobs per month and is still doing repair work. As a low-to-medium-volume shop, joblot sizes range from two to 100 pieces, but most involve single-digit amounts. Turnaround times range from immediately (on the repair service side) to about three weeks on the CNC parts-machining side.
Recent Comments